Home Blog Product Info Everything You Need To Know About Pipe Plugs
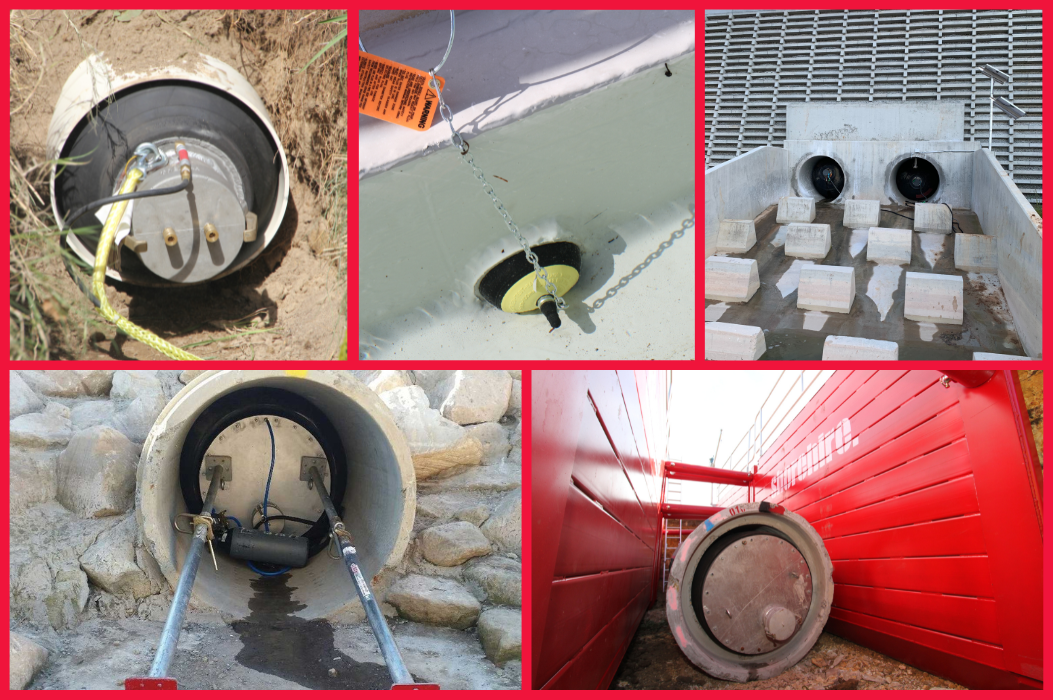
Shore Hire offers the largest range of hireable pipe plugs in Australia, with a huge range of blank, and bypass plugs, as well as a number of industry-leading safety accessories.
HOW DO PIPE TEST PLUGS WORK?
Pipe Plugs are inserted into a pipe and then inflated to the appropriate size, completely filling it and creating a tight, temporary seal. Once the plug is inflated, it can be used for three main purposes: to blank or block off, bypass, or test a pipeline.
They are designed for various applications, including leak locating, bypassing, flow control, and high-pressure or pipeline testing methods using water, air, or vacuum.
Our plugs have been designed for ruggedness, durability, and flexibility while still being easy to use. Our fleet size and diversity means that we are most likely to have a plug that best suits your application, be it high back pressure, high flow or tight access, we’ll have you covered.
WHAT ARE THE DIFFERENT TYPES OF PIPE PLUGS?
Shore Hire has a range of pipe plugs available for hire, each tailored to specific applications:
- Blank Pipe Plugs: These plugs are durable, rugged, and effective in any type of pipe. They don’t have a bypass, and are designed to block or seal pipes for maintenance, inspections, and repairs, completely blocking the flow of water, air, or materials.
- Pneumatic Bypass Plugs: Bypass plugs feature a removal fitting on the top that allows the flow of water or materials to continue through the pipe at a reduced capacity. Made of natural rubber reinforced with polyester cording, these plugs work well in both round and elliptical pipes. We also have a range of “Big Mouth Plugs” to maximise the bypass diameter.
- Pneumatic Test Plugs: These types of plugs are designed to block or bypass sewage flow, as well as conduct low-pressure sewer and stormwater air or water tests. Our range of test plugs can also be used for line acceptance testing, leak location testing, and block flow.
- High-Pressure Test Plugs: These plugs can only be inflated using water, and are specifically designed for use in high-backpressure environments, such as water mains, sewer rising mains, and industrial pipelines. We also have a range of petrol driven Hydrostatic test pumps and calibrated gauges available to hire.
- Water Bypass/Flow Through Sewer Plugs: These plugs divert flow during repair or rehabilitation work while keeping a sewer line in service, and the work area dry, without the need for continuous plumbing. If required, these plugs can also be used as blank plugs by capping off the bypass with a threaded cap or camlock fitting.
Our range of pipe plugs are made from natural rubber and, therefore cannot be used in oil, gas, chemical, or petroleum applications.
We also have a range of pipe plugging accessories to complement our massive pipe plug range, including:
- Mechanical pipe plugs
- Hoses and gauges
- Low-pressure air test kits
- Pumps
- Venturi vacuum test kits
- Vacuum Manhole Testing Plates
- Deflection Gauges and Proving Rings
- Pipe Joint Testing
- High-Pressure Hydrostatic Testing
- Vacuum Pump
- Inspection camera
- Layflat hose
- Inflation pressure alarm system (LP alarm)
- Critical Air regulators and cylinders
- 12v DC compressors for inflating the larger plugs
HOW ARE PIPE PLUGS INSTALLED?
The process of installing a pipe plug can vary based on the type of plug and its application, but some general steps can be followed:
Step 1: Make sure the pipeline is clean and free of debris, obstructions, and pollutants, as well as any damage, cracks, or breaks. Applying pressure to an already damaged pipe can further damage the pipe, potentially leading to the failure of both the pipe and plug.
Step 2: Carefully insert the pipe plug into the pipeline and position it correctly – at least one pipe diameter inside the pipe. Do not allow the plug to protrude from the pipeline while inflating it.
Step 3: Depending on the size of the plug, it could be inflated using a bike or foot pump up to 450mm, or an air compressor for the larger plugs. By using an extension hose, manifold, and gauge, plugs can be inflated from outside the danger zone.
Step 4: Inflate the plug by gradually increasing the air pressure. Check the air pressure gauge to ensure it remain steady throughout the process. Partially inflate the plug, check the gauge, and repeat this cycle until the plug reaches its maximum air pressure.
Step 5: Once the plug is fully inflated, disconnect the pump or air compressor.
Step 6: Brace the plug. Bracing ensures worker safety in the event of plug movement, or an accidental dislodge. This block or brace should be designed to contain a dislodged plug and all materials behind it, should the plug fail during use. Please note that Shore Hire does not offer bracing recommendations or engineering yet.
Step 7: Test the plugs for leaks.
WHAT NEEDS TO BE CONSIDERED WHEN SELECTING A PIPE PLUG?
- The Diameter of the Pipe: Carefully measure the inside diameter of the pipe you’ll be working with – don’t guess/estimate.
- The Pipe’s Minimum and Maximum Sizes Range: Our range of pipe plugs are clearly labelled with their minimum and maximum usage/pipe size ranges. Select the correct plug size for your specific application, and ensure that the maximum backpressure capacity is within the plug’s specified limit.
- The Pipe’s Back Pressure: Back pressure is the pressure that pushes the plug and forces it to move inside or outside the pipeline, depending if it’s a positive or negative pressure we are dealing with. Customers need to determine the maximum back pressure the plug is going to be exposed to, as not all plugs have the same back pressure rating.
- The Length of the Pipe: Different plugs within the same range will have different lengths. For example, a 200mm—400 mm plug may have a 100mm long variant and a 300mm long variant. So, depending on whether you have a longer or shorter pipe and how difficult the plug will be to angle into the pipe, should all be considered when deciding which plug to use.
Every job is different and must be carefully examined to ensure the safest procedure for each circumstance encountered.
HOW CAN YOU STAY SAFE WHEN USING PIPE PLUGS?
- All personnel who use or work in close proximity to test plugs must receive proper training and familiarise themselves with the correct installation, handling, and removal procedures.
- Maintaining consistent and accurate inflation air pressure is extremely important when working with plugs, and every plug should have it’s own inflation hose and gauge to monitor the inflation pressure from a safe distance. Ensure your pressure gauges are accurately calibrated and can maintain a steady pressure setting. Plug inflation pressure must be checked, it’s suggested that pressure is monitored an hour after inflation then every 4 hours after that (pressure in the plug will drop as the plug temperature drops to the pipe and liquid it is exposed to).
- When working with a pipe plug, it’s essential to avoid the Danger Zone. This zone is located directly in front of the pipeline and plug, forming an invisible, funnel-shaped area that increases in size as it moves outward from the plug. If the plug fails, it and any debris will launch outward with tremendous, potentially deadly force.
- It’s vital that you inspect a pipe plug before use. Although we conduct our own inspections of our pipe plugs, it’s also important for you to examine the plug for any damage before putting it into service. Damage can include, but is not limited to, cuts, abrasions, punctures, bulges, cracks, corrosion, loose or damaged fittings and components, and leaks.
- Do not over-inflate or under-inflate a pneumatic plug. Over-inflating a plug beyond the required pressure or under-inflating it to less than the necessary pressure can cause the plug to either move, rupture, or dislodge at extreme velocity. Improper inflation can cause plug failure or dislodgement, potentially resulting in death, serious injury, or property damage.
- Pneumatic Plugs are only intended for temporary sealing and should only be used for the short duration necessary to complete the task. If a pneumatic plug must be in place for an extended period, the inflation pressure should be checked and adjusted. We suggest using the critical air regulator and cylinder, and the low inflation pressure alarm in these situations.
If you would like to learn more about our range of Pipe Plugs, or any of our pipe plugging accessories, visit your nearest branch, email [email protected], or call our friendly team of experts at 1300 SHORE HIRE.